During the formation evaluation process, operators evaluate the well and decide whether or not it is worth completing. The completions process prepares the well for the production phase of operations, when hydrocarbons are actually taken out of the ground, processed, and sold.
The completion process occurs in several stages. These can be divided as follows:
- Planning
- Casing cementing and inspection
- Well stimulation
- Completion types
- Downhole equipment and tubing installation
- Surface equipment installation
In this section, we’ll provide an overview of each of these steps.
Planning for Completions
Once a decision has been made to move ahead and prepare a well for production, some additional details need to be ironed out. For example, will the bottom of the well be left open to the producing formation, or will casing need to be installed to prevent formation collapse or the production of sand? Will there be one producing zone or multiple zones from which to produce? Will stimulation techniques such as hydraulic fracturing be applied? If so, to which zones?
These decisions are business decisions that are usually made after a cost-profit analysis. They are made based on knowledge of the formation gained during the exploration, drilling, and formation evaluation phases of oil and gas development. Additionally, lease ownership can play a role in the determination of multiple depth completions.
Once the future production plan is finalized, completion operations can begin.
Ensuring Casing Integrity
Before completion and, ultimately, production operations can get underway, operators need to make sure that the casing is structurally sound and securely bonded with cement to the borehole walls. If the well will have an “open hole” completion, the casing will only extend to the top of the producing zone. For a fully-cased well, the casing extends all the way to the bottom (or end in a horizontal well) of the hole.
The primary method for casing evaluation is the use of cement bond logging tools, which are acoustic (sonic) tools. The following figure shows the basics of a bond tool response (right side) compared to the casing and associated cement1USEPA (2013) Study of the Potential Impacts of Hydraulic Fracturing on Drinking Water Resources: Summary of April 16–17, 2013, Technical Workshop on Well Construction/Operation and Subsurface Modeling and June 3, 2013, Subsurface Modeling Technical Follow-up Discussion. Retrieved 4/20/21 from https://www.epa.gov/sites/production/files/2013-10/documents/summary-technical-workshop-well-construction-operation-subsurface-modeling.pdf. The “TOC” or top of cement is noted. If you look to the right of the figure, the acoustic traces are smeared across the cemented portion of the well. Whereas, the pipe that is not cemented, frequently referred to as “free pipe” shows very distinct sonic traces as the free pipe ‘rings’ as part of the logging process. The “triangle” points in the center track indicate where casing collars are located.
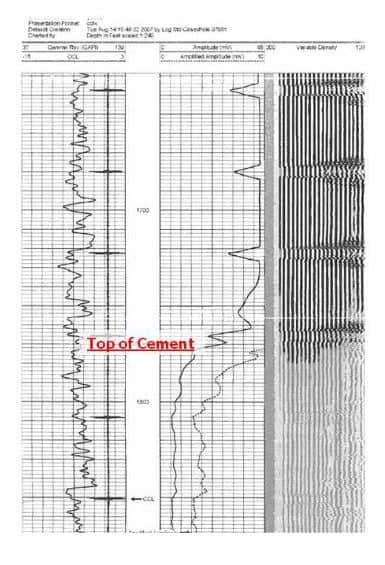
- USEPA (2013) Study of the Potential Impacts of Hydraulic Fracturingo n Drinking Water Resources: Summary of April 16–17, 2013, Technical Workshop on Well Construction/Operation and Subsurface Modeling and June 3, 2013, Subsurface Modeling Technical Follow-up Discussion. Retrieved 4/20/21 from https://www.epa.gov/sites/production/files/2013-10/documents/summary-technical-workshop-well-construction-operation-subsurface-modeling.pdf
Stimulation
During the completion process, stimulation of the subject reservoir might be required. Two types of well stimulation, hydraulic fracturing and acidizing, are the most common techniques used. Depending on the details of the specific method being used, the timing of stimulation within the completion process may differ..
We’ll get into the details of simulation methods in the next lesson.
Completions Types
One of the most important parts of the completion process is the preparation of the producing section of the well bore for production. This typically involves the installation of equipment to provide a conduit for hydrocarbons to enter the well bore, prevent the intrusion of sand from the reservoir, and allow for the isolation of different producing zones.
There are three classes of completions.
Open Hole
In an open hole completion, the well is cased only to the top of the producing zone. No equipment is installed across the producing zone – formation fluids are allowed to flow directly into the well.
Open hole completions have the disadvantage of having no mechanism for preventing sand production and ensuring wellbore stability in the producing zone. When loose sand enters the production casing, forced upwards by the pressure of formation fluids and gases, it acts like a sandblaster inside the pipes and can wear and erode them away quickly, resulting in leaks or destroyed valves. Understanding the pressures at which sand will be produced is important for maintaining the integrity of the well.
While there are risks, open hole completions are significantly cheaper than lined or cased completions. Open hole completions are ideal for strong, well-lithified producing units where failure of the borehole walls isn’t anticipated and is not a major concern.
Liner
In a liner completion, the well is cased to the top of the producing zone. Then, a liner, usually designed to filter sand out of the hydrocarbons, is hung from the bottom of the last length of well casing and extended across the length of the producing zone.
This method is used in situations where an open hole completion is preferable to a cased completion, but sand production would become an issue if the hole was left completely open.
One disadvantage of the liner completion is that it makes it harder for exploration and production companies to selectively stimulate certain zones of the producing formation while leaving others untouched. Additionally, the diameter of the producing zone is decreased, which results in a lower pressure drop into the wellbore and potentially slower production rates.
Cased
Cased hole completions are the most common type. In a cased hole completion, casing is installed and cemented across the entire producing zone, completely sealing the wellbore off from the surrounding rocks. Of course now hydrocarbons can’t enter the well, andthe production casing needs to be perforated at selected locations, to allow fluids to enter the wellbore. Perforation is most often completed with a perforating gun, which shoots small metal bullets or explosive charges (forced air) through the metal casing and cement lining of the wellbore, creating holes through which the hydrocarbons can flow. Cased completions are more expensive than open hole completions due to the need to perforate and the additional casing costs, however, they provide more control during the life of the well and the ability to seal off watered out zones.
Downhole Equipment and Tubing
Once the bottom of the hole is prepared, it’s time to create a path for hydrocarbons to flow to the surface. In most wells, specialized production tubing is run from the top of the producing zone to the wellhead. This smaller diameter tubing provides an additional barrier between the well and the surrounding rocks and protects the well casing from corrosion. It also increases the potential for natural lift within the wellbore. Unlike casing, tubing is not cemented in the well and is removable and replaceable as needed
The production tubing is frquently attached to a packer at the top of the producing zone. The packer squeezes against the wellbore or casing walls and forces hydrocarbons to flow into the production tubing rather than through the annulus between the production tubing and the casing.
In wells with more than one producing zone, the producing zones may be connected by multiple strings production tubing. This allows the parts of the well that aren’t producing to be bypassed. Packers and tubing can also be used to bypass damaged or corroded sections of casing.
In additional to tubing and packers, other downhole equipment such as pressure gauges, seating nipples, and sliding sleeves may be installed in the well. There are multiple reasons for installing such but are too numerous to mention here.
Surface Equipment
During the completion and production process setup, a variety of equipment might be brought in at the surface. Some main stay to help with well production, while other equipment is only brought in for specialized services.
For example, if stimulation techniques such as hydraulic fracturing or acidizing are utilized, an entire new set of equipment including pumps, blenders and supply vehicles will be brought in to the well site. Once the stimulation treatment is completed, this equipment is removed.

Operators will install a wellhead or “Christmas tree” at the top of the well. The Christmas tree, named for its (supposed) resemblance to the holiday decoration, consists of a sequence of valves and pipes. Its purpose is to control the flow of hydrocarbons from the well and allow access to the various annuli (casing-casing and tubing-casing) to allow for the monitoring of pressures. The casing and tubing strings are “landed” in the Christmas tree using wedges for easy accessibility by a workover rig.
Once the completion process is done, the above-ground portion of a well site may consist simply of a wellhead and possibly a pump.
At this point, the well is then “turned to production” or allowed to initiate production. Additional equipment, such as separators and tanks, may be brought to the site to process and store produced hydrocarbons. We’ll cover this process in the production segment of the course.
Images: “Triplex Tree” by Jim Ladlee for Top Energy Training; “Picture of an oil wellhead with multiple heads” by Huyangshu via iStock